What is the future of 3D printing? Away from the hype and Wall Street, what are we really going to be able to do? What are the challenges of additive manufacturing (AM)? Will we be a niche application technology? Or will we be used in conjunction with mass production? Will we be used everywhere? Or only in a few industries? We asked some key 3D printing industry leaders to think about the future of AM and compiled their responses
We used to believe that 3D printing would replace traditional wholesale manufacturing. Now, that is no longer the case. 3D printing consultant Oliver Smith of ReThink Additive noted:
“AM will never replace high-volume manufacturing in a similar scenario, i.e. producing the same parts with 3D printing instead of injection molding. Where it will almost certainly become a large-scale manufacturing technology will be when we innovate and design products and applications where the capabilities of 3D printing massively compress the process chain or add extremely superior functionality that cannot be equaled by conventional production methods. For example, custom ergonomic orthoses and prostheses, orthopedic implants with highly fitted lattice structures, or direct dental aligners produced directly from scanned data.
Here, Oliver focuses on use cases where 3D printing really makes sense. An easily overlooked point he makes is that FA could be very useful in cases where we are “compressing the process chain”. Time advantages aren’t the only ones that make our technology meaningful. We could also benefit from places where the space, or the number of steps, or the waiting for tooling, or the capital needed, or the number of parts needed would be too great with conventional alternatives. It’s something that isn’t often viewed so holistically.
You could really be missing out on many of the key benefits of AM if you think of it as if time were the only process-related variable. Think of 3D printing on the moon, in clean rooms, aboard oil rigs, in top-secret projects, in ITAR or other heavy regulatory regimes and you will see more benefits than just “faster”.
Oliver’s second point of adding higher capabilities to a part is now almost orthodox, with many believing that key geometric advantages, such as unique structures or N=1 products, are key for our future. However, if we really want to manufacture these things at scale, what are the challenges?
A complex fluid manifold, optimized using 3D printing. (Image courtesy of 3D Systems)
Dr. Brent Stucker, chief scientist at 3D Systems, told 3DPrint.com:
“Traditional manufacturing is fast and cheap once a custom mold or tool has been made for a certain geometry and/or once a milling machine has been programmed to make a specific part. This is especially true for simple shapes. For complex shapes or parts produced at low volume, AM is already competitive. But AM needs to get faster and cheaper to compete with traditional mass manufacturing of simple shapes.
One of the challenges of AM is that many designers have learned to design parts within traditional manufacturing constraints. This leads designers to create complex systems as a set of simple parts put together. For manufacturing with AM to be better than traditional manufacturing, designers must consider the ability of AM to create extremely complex geometries as a single construct integrated into an AM machine. The more designers push the boundaries of performance improvement and part consolidation by leveraging its ability to deliver complex geometries, the more AM makes sense over traditional manufacturing.
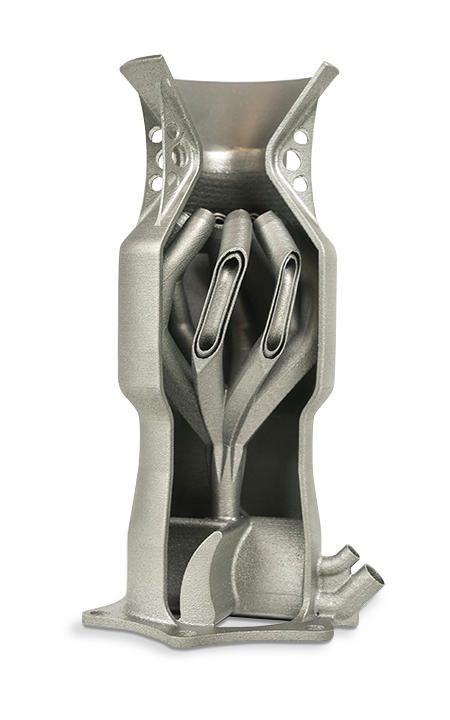
AM combustion chamber. Image courtesy of 3D Systems.
Brent’s answer seems deceptively simple at first, referring to the oft-cited reasons for moving to 3D printing, such as upfront costs and faster tool production. The lack of design sensitivity and familiarity with AM is definitely holding us back.
However, where Brent really makes a very elegant point is when he refers to “complex geometries partially consolidated into a single AM construction.” This is another wonderfully accurate concept that is often overlooked. People think that builds, parts or assemblies are expensive, but if you optimize components for builds and embrace complexity, then the whole product could be made in a new way in which 3D printing is immediately more profitable. Often we try to use an expensive machine to print a kickstand when we could 3D print the whole wheelchair.
Pat Carey, senior vice president of strategic growth at Stratasys, thinks the lack of additive skills is a big problem.
“Career opportunities in additive manufacturing far exceed the rate at which people are trained for positions. We have partnered with trade schools, universities, professional and educational organizations, as well as teaching schools to encourage the development and delivery of additive manufacturing education and training,” Carey said. “Our customers also feel the need for more training. For example, a large car manufacturer is looking to open a large plant and they have asked us to partner with them to host a recruitment event for a plant that won’t be ready for a certain number. of years. By hosting the event now, the automaker can encourage future employees to get the training needed to take on an AM position at the plant. We also see the need for role-specific training as additive applications specialize more in dental, medical, engineering, design and tooling.
This sentiment is often shared by many in our industry and I really like the idea of planning ahead and trying to inspire people to be ready when opportunities arise. A hugely important point that Pat also makes is that companies often have no idea how to calculate the efficiency of 3D printing for them.
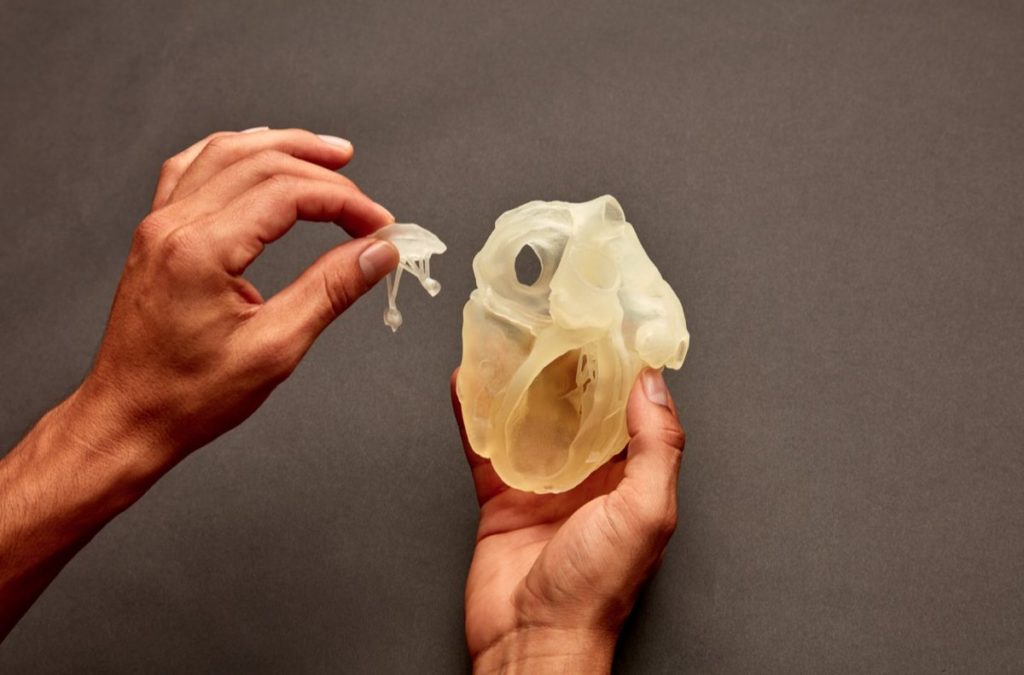
Medical 3D printing with the Stratasys J750 digital anatomy printer. Image courtesy of Stratasys.
“Companies also need help defining the ROI/business case of how AM will benefit their manufacturing operations and how to execute it,” Carey said. “We know the technology works, but customers need to be guided as to which technology, materials and applications are best for them, how much additive parts cost versus traditional parts cost, how to develop a return on investment on more of the manufacturing process, the value of part consolidation and the reduction of labor costs.”
Without knowledge of AM, companies often charge incorrectly. My favorite example is the “tears in the boardroom” scenario, in which an AM project falls apart at a late stage due to mundane issues such as not accounting for sufficient spacing between rooms in the build room or not knowing that a machine has eight hours of turnaround time between builds. It seems silly that intelligent people can sometimes not know such essential things, but obviously they are only essential if you know them. This is an important point to make because, by arming companies with the correct information, we could really help accelerate their adoption of 3D printing.
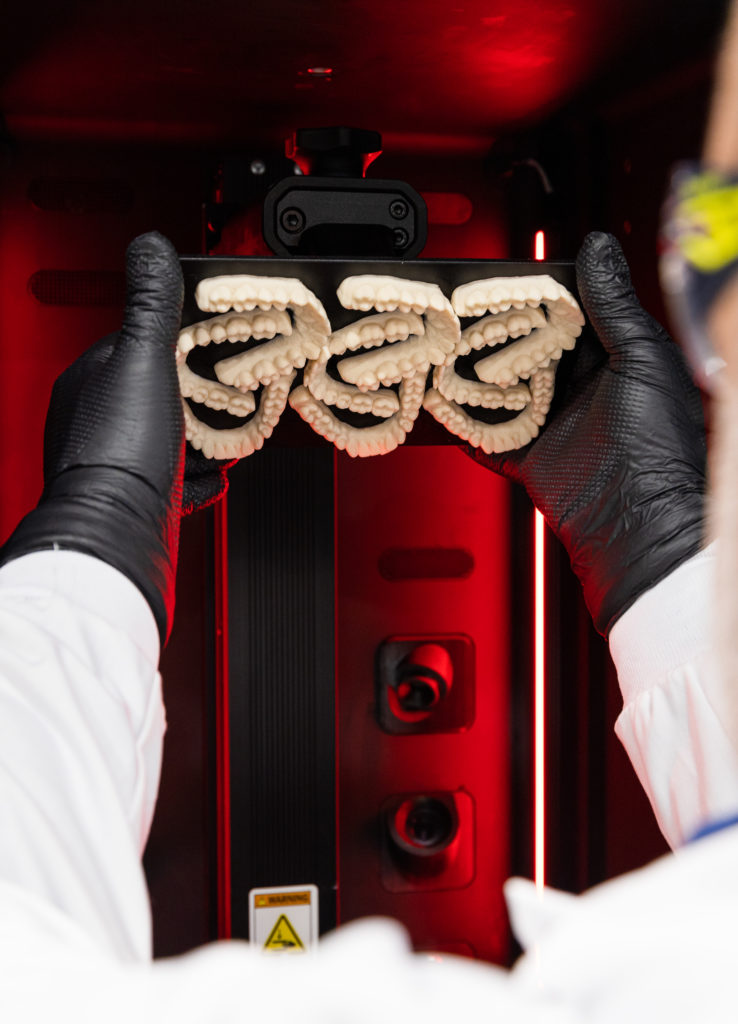
The Origin One Dental machine in a dental laboratory. Image courtesy of Stratasys.
Another idea that Pat brought up is “to eliminate bugs for large-scale connectivity”:
“Manufacturers continue to embrace Industry 4.0 and the IIoT, with connected 3D printers being just one piece of this puzzle. Companies should continue to partner with their IT teams to demonstrate the uses of a 3D printer, or fleet of printers, for manufacturing, as opposed to just an engineering tool.
This is something that I don’t think many take into account enough. We now know that 3D printing will not replace everything, but at the same time we still act like 3D printing is an island. We have far too few methods by which we can integrate with ERP, other tools, other applications, and the business as a whole. We have an “enterprise 3D printing” industry with no way to integrate these 3D printers into the enterprise. If we really want to manufacture, we have to play with all the manufacturing infrastructure that exists in a company.
We’ll check with our experts in a later post to see what else they found for us.
Subscribe to our newsletter
Stay up to date on all the latest 3D printing industry news and receive information and offers from third-party vendors.
More Stories
Delay in mass production of new Intel products is a boon for AMD, share of AMD x86 server processors expected to exceed 22% in 2023, according to TrendForce
Quantum industry milestone brings mass production of quantum chips closer
NEO Battery Materials provides updates on installation of additional equipment for mass production optimization and final stages of commercial plant design for construction