Former vice president Al Gore told an audience attending a conference at Desktop Metal (DM) in March that the acceptance of new technologies usually takes longer than expected. And often, old ways have to be abandoned before a new technology can gain traction.
Gore cited 3D printing as an example. “So many changes had to take place before 3D printing could be accepted,” he said. “Infrastructure. Thought. Designing parts that could unlock the potential of 3D printing. “It took a long time.”
It also takes time to develop, test, tweak, retest, retweak, and qualify a new 3D printer, especially one that innovates as much as DM’s production system. The company claims its new machine is “the world’s fastest metal printer…and the first and only metal 3D printing system for mass production that [can] compete with traditional manufacturing processes.
The printer builds parts four times faster than other binder jetting systems and 100 times faster and 20 times cheaper than laser-based styles.
The first unit was installed in the first quarter of this year at one of DM’s early partners, a Fortune 500 public company. It plans to deliver a “handful” of additional systems through the end of 2019 and accelerate deliveries in 2020.
The four-year-old Burlington, Massachusetts-based manufacturer launched a smaller, low-volume metal 3D printer in 2017 called the Studio System. Later that year, the company began designing and testing various iterations of the production system.
Excitement about the system has intensified in the industry and among investors since its launch was announced. The company has received $438 million in funding to date and its current market valuation is estimated at $1.5 billion.
Pioneering spirit
DM CTO and co-founder Jonah Myerberg described the journey from concept to launch as “a product of working with pioneers (early partners) to figure out what they really want, what’s important. for them and then scale the printer to meet their needs.”
Larry Lyons, VP of Product, added, “We’ve been very selective in the types of companies we work with. We choose partners from whom we think we can learn a lot, in addition to bringing them up to date with the production. »
The production system’s metal 3D printer is said to build parts four times faster than other binder-jetting systems and 100 times faster than laser-based models.
Part of DM’s commitment to partnering with its customers is to reach a point where controlling a production system is like controlling a CNC milling machine or an injection molding machine. If that happened, Lyons said, it would be a big step toward achieving one of the company’s overarching goals: “Transforming the manufacturing market.”
A transformative metal 3D printer should be as easy and predictable to use as a CNC milling machine. “We need to achieve a high level of reliability and ease of access and installation to truly disrupt this massive market,” Lyons said. Highly specialized printers take time to operate and require intensive engagement, he added, making them unable to disrupt the $12 trillion global manufacturing market.
How it works
Printing parts in production involves four steps:
1. Print. Above the 750 x 330 x 250 millimeter build envelope are two full-width print bars. They are equipped with a total of 32,768 piezoelectric inkjet nozzles that disperse metal powder at a rate of 3 billion drops per second.
Each pass lasts approximately 2 seconds, during which the nozzles deposit a layer of powder 50 microns thick. The average manufacturing speed is 12,000 cubic centimeters per hour, which is equivalent to printing 60 kilograms of metal parts per hour.
2. Removal of the solvent. The build box containing the printed parts is placed in a chamber where the solvents are removed and the binder materials solidify, a step that strengthens the parts.
3. Powder. The parts are removed from the build box and cleared of loose powder.
4. Sintering. The parts are heated in a furnace to near melting temperatures, which removes any residual binder and causes the metal particles to melt and densify.
Two key technologies underpin the production system: binder jet, developed by DM co-founder Emanuel “Ely” Sachs and colleagues at MIT, and single-pass inkjet, invented by scientist Paul Hoisington inkjet systems.
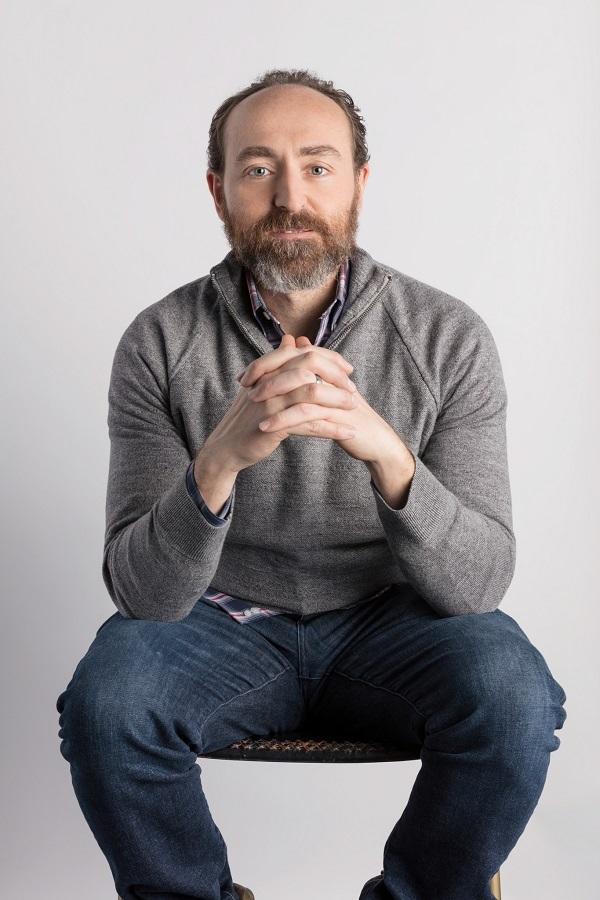
Desktop Metal CTO Jonah Myerberg said the industry “has been patiently waiting for metal 3D printers to decline in cost and complexity, as plastic 3D printers have over the past 20 to 25 years. “.
With Single Pass Jetting (SPJ), as DM calls its powder dispensing process, the bidirectional printhead accelerates to maximum speed, maintains speed for a brief period, decelerates, and then reverses direction.
A modification to the original design was to extend the bed so that each pass lasted a bit longer. “It stabilized the process without over-complicating things,” Myerberg said.
Maintaining consistent layer thickness over a relatively large area using fast-moving printheads has proven difficult. Myerberg said a solution has been found, one that maintains a layer thickness tolerance of around 2 µm.
He added: “If you look at the print box, you will see that the powder is not completely flat. But that’s okay, as long as any slight ripple repeats exactly over and over and over again.
Myerberg likened SPJ to 2D printing large flat surfaces. “It’s the same technology used for the inkjet presses used to make billboards,” he said, “except we’re using 2D printing to create this image at very high resolution above a large box full of powder.”
Another design feature that speeds up production is placing part solidification functions in an oven downstream of the printer. “This allows the printer to focus solely on producing powder metal parts that are held together with a binder material,” Lyons explained. “By separating printing and heating, we’re able to achieve a much, much faster system. This is where the 100x faster comes from.
Two other time-saving aspects of the system are the materials of construction it uses and patented technology that minimizes post-processing of parts.
Instead of expensive build powders that are expensive and need to be qualified, Production System manufactures parts from MIM (metal injection molding) materials. They are relatively inexpensive, readily available, and there is a huge selection to choose from.
A significant barrier to the widespread acceptance of 3D printing is the post-processing required to prepare a part or product for use. With metal printers, parts weld themselves to their build plate, which often must be carefully removed on a machining center or wire-cut EDM machine. This adds time and cost and negates the benefits of mass production.
“We didn’t want to provide a solution that would get you three-quarters of the way [to mass-producing parts] and then let you figure out what other gear you need to get to 100%,” Lyons said.
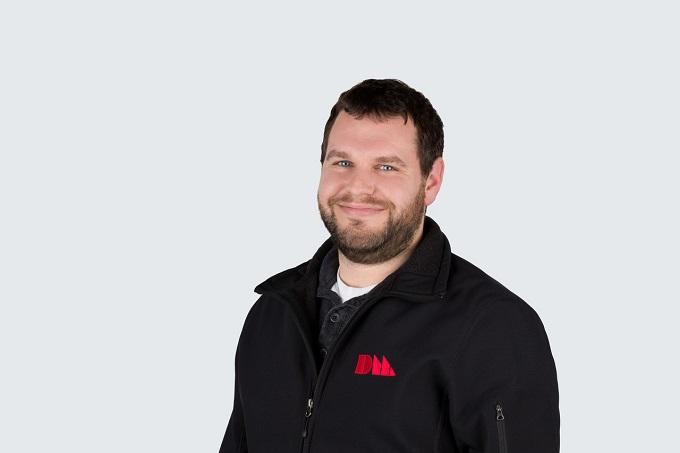
One of the company’s goals is to “transform the manufacturing market,” said Desktop Metal vice president of product Larry Lyons.
To ease the pain of post-processing, DM has developed the “separable support interface layer” technology. Traditional powder bed laser printers are limited to one material per build cycle. The production system, meanwhile, allows the use of several materials. This allows the user to print support structures that do not stick or consolidate with parts during sintering, making them easily removable by hand.
The interface technology doesn’t completely eliminate post-processing, Lyons noted. “If you need a surface finish of less than 20µm, you’ll need to polish the part, just like you would with casting or another high-volume method.”
“Accessible” Technology
Does a printer that makes parts 100 times faster and 20 times cheaper than a conventional system cost more?
The cost is comparable to laser-based metal systems, according to Myerberg. The Studio System+ printer retails for $60,000, and full system hardware is available for $160,000. The production system is modular and configurable and the price is based on customer requirements. The printer sells for $750,000.
“We really want to make metal printing accessible to everyone, and these systems are very accessible,” Myerberg said.
He added that the industry is “patiently waiting for metal 3D printers to decline in cost and complexity, like plastic 3D printers have over the past 20 to 25 years. And now that it has happened, there is a lot of excitement.
More Stories
Floating Production System (FPS) Market will See Booming Opportunities for Growth and Development By 2030 | BUMI Armada Berhad, Daewoo Shipbuilding & Marine Engineering
Isotope Production System begins commercial production of
Didimo Announces $7.15M Funding to Expand 3D Avatar Production System